The Science Behind Porosity: A Comprehensive Guide for Welders and Fabricators
Recognizing the detailed mechanisms behind porosity in welding is important for welders and fabricators aiming for impeccable workmanship. From the structure of the base products to the intricacies of the welding process itself, a multitude of variables conspire to either worsen or ease the existence of porosity.
Comprehending Porosity in Welding
FIRST SENTENCE:
Exam of porosity in welding discloses vital insights into the stability and top quality of the weld joint. Porosity, identified by the presence of dental caries or spaces within the weld steel, is a common issue in welding procedures. These gaps, if not correctly resolved, can jeopardize the architectural honesty and mechanical residential or commercial properties of the weld, causing potential failings in the completed product.
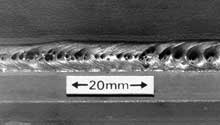
To find and measure porosity, non-destructive screening methods such as ultrasonic testing or X-ray examination are typically used. These techniques permit the recognition of inner defects without compromising the honesty of the weld. By assessing the size, shape, and distribution of porosity within a weld, welders can make enlightened decisions to enhance their welding processes and accomplish sounder weld joints.

Factors Influencing Porosity Formation
The event of porosity in welding is influenced by a myriad of elements, ranging from gas shielding performance to the details of welding criterion settings. Welding criteria, including voltage, existing, travel rate, and electrode kind, likewise impact porosity development. The welding strategy utilized, such as gas steel arc welding (GMAW) or protected metal arc welding (SMAW), can affect porosity development due description to variants in heat circulation and gas insurance coverage - What is Porosity.
Effects of Porosity on Weld Top Quality
The existence of porosity additionally compromises the weld's resistance to rust, as the caught air or gases within the gaps can react with the surrounding environment, leading to deterioration over time. In addition, porosity can prevent the weld's capacity to stand up to pressure or effect, more jeopardizing the total high quality and dependability of the bonded framework. In crucial applications such as click resources aerospace, auto, or structural buildings, where safety and toughness are paramount, the destructive effects of porosity on weld quality can have serious consequences, highlighting the value of minimizing porosity with proper welding techniques and treatments.
Strategies to Reduce Porosity
In addition, using the suitable welding parameters, such as the correct voltage, current, and take a trip rate, is crucial in stopping porosity. Keeping a constant arc size and angle during welding also assists lower the probability of porosity.

Utilizing the ideal welding technique, such as back-stepping or employing a weaving movement, can additionally help disperse warmth uniformly and minimize the possibilities of porosity formation. By applying these techniques, welders can effectively decrease porosity and create top notch bonded joints.
Advanced Solutions for Porosity Control
Implementing advanced innovations and ingenious approaches plays a crucial role in achieving remarkable control over porosity in welding processes. Additionally, employing sophisticated welding methods such as pulsed MIG welding or modified ambience welding can likewise aid minimize porosity concerns.
An additional innovative service entails using innovative welding equipment. For circumstances, using tools with integrated features like waveform control and sophisticated check this source of power can improve weld high quality and reduce porosity risks. In addition, the execution of automated welding systems with exact control over parameters can significantly lessen porosity defects.
Additionally, integrating sophisticated tracking and evaluation innovations such as real-time X-ray imaging or automated ultrasonic testing can aid in finding porosity early in the welding process, permitting instant rehabilitative actions. On the whole, integrating these advanced services can considerably improve porosity control and enhance the overall quality of welded parts.
Final Thought
In final thought, understanding the science behind porosity in welding is necessary for welders and fabricators to produce top notch welds - What is Porosity. Advanced remedies for porosity control can even more boost the welding procedure and make certain a strong and trusted weld.